The New Model of Distribution of Recaptured Building Materials
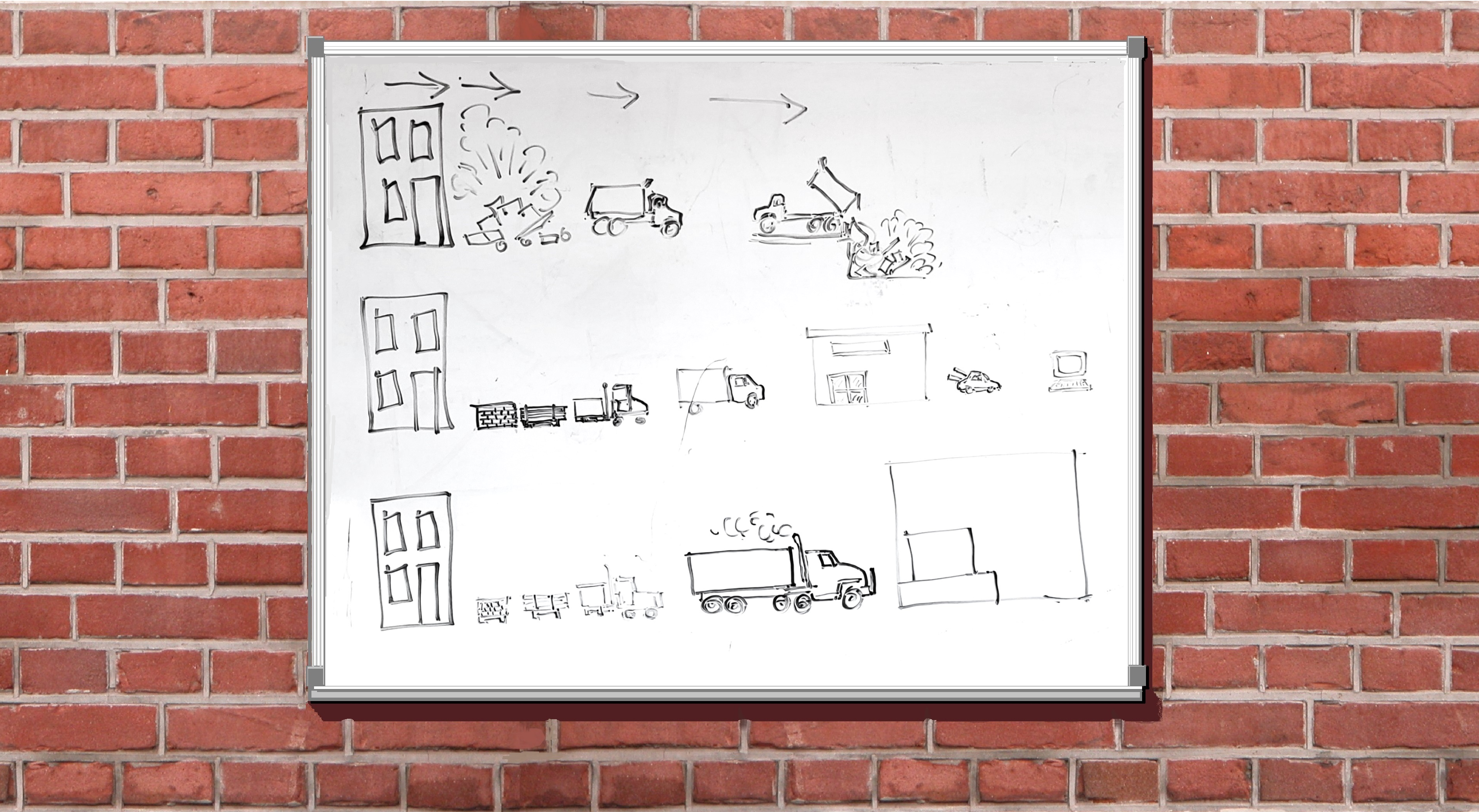
Here’s the problem: Construction & Demolition Waste is the largest source of “waste” materials in America. This sector creates two times more waste every year than ALL the trash and garbage thrown away by all 330,000,000 Americans all year long. And, it’s growing faster than all the efforts to stop it.
The current model of capture and distribution of used materials is inadequate.
We are proposing a solution.
First, let’s look at how buildings are treated at their “end-of-life.”
- For the sake of not creating waste or using energy that may not be necessary, reuse of a whole building is ideal. Reuse of the entire building must be considered carefully as the ultimate option for sustainability. If a building can be renovated, updated, remodeled, retrofitted, or given an alternative use, this eliminates the potential of creating waste. There are other benefits, as well, subjects for another time.
- When a building owner decides to remove a building from its site, the typical process is to demolish the building with heavy equipment or with a combination of explosives and then heavy equipment for tall or very large buildings. Then, the demolished materials are hauled away and disposed of in landfills.
- Pre-demolition, occasionally buildings are partially dismantled for materials like wiring and electrical, plumbing, cabinetry and woodwork, tile, stone, terra cotta ornamentation, and other materials valued for their resale value.
- Mid-demolition, occasionally demolition halts temporarily and assists with removal of such structural materials as trusses, columns, beams, joists, and other large structural elements and components for reuse.
- Post-demolition, there can be a variety of materials that are separated to be sent to recycling facilities. Most common of these are concrete, steel, and heavy wood timbers. Concrete is typically crushed and used as aggregate for new concrete, or it is used directly as fill material. Steel is typically treated as scrap metal and sent to be melted down and made into new products.
- As a means of minimizing waste creation and optimizing reuse over recycling and surely over disposal, deconstruction is the choice. Deconstruction is the careful dismantling of a building to salvage its materials as close to entirely as possible so that they may be reused in their current state. This allows these materials to be donated or sold for new uses.
There is a system of distribution of salvaged building materials for reuse in place now. It has been around for decades. Essentially it consists of the following:
- Those who deconstruct or remove building materials and make them available to be reused.
- Generally, in the United States, residential buildings are by far the most frequently deconstructed, with only a tiny percentage of commercial or institutional buildings being deconstructed. This is changing slowly, with more commercial deconstruction.
- Some materials can only be recycled, like scrap metal, some glass, asphalt shingles, gypsum wallboard, and concrete foundations and these can be carefully separated on-site.
- The reusable materials may get donated to a non-profit organization and the building owner or downstream owner of the materials may be able to realize a legitimate tax deduction for the donation, based on an appraisal of the market value of the materials, either prior to or after they are removed from the structure.
- The reusable salvaged materials typically go to either a retail salvage store, a wholesale used lumber broker or seller, or a remanufacturer of specific materials such as wood or doors. The salvage stores are the largest volume distributors.
- The “channels” through which used materials are sold within the salvage store model are, ranked by volume from highest to lowest:
- Walk-in retail – This is the most common way to purchase these materials and it generally severely limits the reach of the sellers to their potential audiences.
- Online presentation of merchandise – Sellers display their merchandise on websites, marketplaces, and social media to get attention and interest to encourage shoppers to come to their stores. This still requires shoppers to shop in-person, or to have the seller compute and transact shipping charges in a separate transaction, usually over the phone.
- Online sale of merchandise – ecommerce – Only a very small percentage of used building materials are purchased through a complete online transaction taking into account weight and dimensions of the materials and origins and destinations to compute shipping costs.
- The “market” or “audience” for retail sales of salvaged materials consists almost entirely of residential and small-scale commercial purchases. Buyers are homeowners, craftspeople, furniture makers, and professional designers who purchase materials on behalf of their clients.
This system, as a working model of distribution, is insufficient and unwilling to grow, despite a small percentage demonstrating willingness to expand and adapt. Whoever is willing can surely be part of this expansion.
Here is what is missing in the current model of distribution and what must be included in the new model:
- Multiples of current Volumes – This means creating high processing throughput along with storage of inventory of desirable variety, as desired by the “demand” audience of real buyers.
- Processing capacity – High-speed production done efficiently in large processing facilities.
- Modern systemization – Unity of categorization, adoption of the existing technology employed by the AEC community and implementation of new technologies to augment the adoption and integration of salvaged materials into new construction.
We must develop a new model that can expand to multiples of current distribution capacity.
We at ReCapturit have envisioned a simple and holistic approach to the entire ecosystem of building materials reuse that can offer a unifying objective to the industry.
- It connects and coordinates countless independent efforts around the nation.
- It includes technology, Architecture, Engineering, and Construction, policy, planning, warehousing, job creation, deconstruction, urban mining, supply chain, tax benefits, plus real estate, building owners, and more.
- It provides ample selection and quantities of materials, in formats that Architects can use to model and specify, builders can purchase confidently in their usual channels, and owners can enjoy the benefits of genuine sustainability with retained or enhanced profitability.
- All this happens at a greater scale, with higher capacities, efficiencies, and production capabilities, at lower costs, to provide consistency of supply for the currently dormant demand.
- Many pieces are already in place.
- Remember, change is not easy. Engage with the eager and willing and the rest will follow.
Start at the five main sources. Each of these has its own processes for moving materials toward processing:
- Demolition
- Construction Jobsites
- Deconstruction
- Urban Mining
- Discontinued, Overages, Returns, and Seconds as Inventory (DORSI)
Funnel materials into Processing and storage facilities:
- MRFs – Materials Recycling Facilities. These go by several names and acronyms, like recycling centers, resource recovery facilities, recycling plants, waste recovery facilities, materials recovery facilities (MRFs), and recycling depots.
- Reuse Innovation Centers (RIC) – This is a concept developed by Deconstruction veteran, Dave Bennink of Reuse Consulting, a 30+ year deconstruction company and consultancy owner. The RIC is a combination of local warehouse, processing, remanufacturing, and distribution center located in or near an urban area that combines the salvage store model with on-premise upcycling and repurposing of materials, with potential of classes and training. “It is a business cooperative of sorts, with 10 or more circular businesses working together in a synergistic way.”
- TDC – Transformation Distribution Center™ - ReCapturit’s solution for reuse rather than recycling. This is a regional commercial processing and warehousing facility with no retail component. This outlines what needs to be completed at this phase in this new model of distribution (whether at a TDC or another facility):
- The TDC combines all the usable would-be-waste materials for processing and warehousing from the five main sources (mentioned above).
- This is a wholesale facility, processing large-scale quantities of materials, sorting, cleaning, identifying, photographing, weighing, then inputting each item into the warehouse inventory, classifying, fully describing, and then giving a unique identifier (bar code, QR code, RFID code, SKU number, etc.) to each item (or lot).
- Materials in the TDC are palleted, boxed, banded, or packaged into shipping quantities and containers for wholesale distribution.
- Once in the system, the materials are now inventoried and can be stored, sold, even donated (potentially, given the right organizational structure).
- From the TDC, processed materials can be sold wholesale via ecommerce. Some potential buyers can be:
- Retail salvage stores
- Builders and Building Contractors – commercial, residential, industrial
- Building owners
- Retailers and wholesalers of building materials
- Strictly used materials, as in a used lumber wholesaler.
- New and used together, as in a Home Depot or Lowes (aspirational, yes, but highly likely given adequate consistent volumes and quality).
- Architects and engineers can also SPECIFY these materials now that used materials are made available in the technology and sales channels they use.
- Some materials are moved on to recycling or to disposal when no other option is available.
This brings up another aspect of the New Model of Distribution: Customer Development. Customer Development, according to Cindy Alvarez, author of Lean Customer Development – Build Products Your Customers Will Buy, defines this as “…an approach to reduce business risks by challenging assumptions about who the customers are, what they need, and why and how they buy. It involves understanding the customers' needs and pain points, and delivering solutions to them. The process includes applying the scientific method to learn about your customers, which can help confirm that you're on track to a business model that works and a product that people want to buy.”
“A product that people want to buy.” This has often been overlooked because it appears complicated. It need not be.
Who will buy used materials in greater quantities? Who will buy these larger quantities of recaptured building materials if made available in the quantities and qualities they need, at the timing they demand, specified by architects and engineers within referenceable categorization structures they use, that can be purchased in the means they are accustomed to? That question has been largely unasked.
We are asking it now.
To access and entice higher-volume buyers of building materials for commercial projects, we need to understand the sequence in which those products are chosen and purchased, and then adapt to those processes, not expect the community of architects, engineers, construction companies, and building owners to adapt to… to what? The technology of the used materials sector? There is none. So, we must adapt and conform to theirs.
We must connect to Revit, BIM systems, the Master Format, 3D modeling systems, LiDAR and other scanning technologies, and new apps that access used materials and put them into the same systems architects already use.
In addition to that, using the methods of Customer Development, we must connect with and communicate with the AEC community and find the materials they will most readily be able to include into new construction designs and specifications that their clients want. Start simply.
What do building owners want? We must ask them, too.
We must be mindful of profit. Profits dictate materials choices. Cheaper usually wins. Can we, the recaptured building materials industry provide equivalent materials that can be substituted for new? What do the building owners want? What are their architects and designers and engineers recommending and why? What can we provide - consistently?
What are the strong selling points of used?
- Price?
- History?
- Story?
- Sustainability?
- Lack of supply chain issues (that is definitely a strong point!)?
- What if we could deliver on all of them and get real financial gains with “soft” gains as well?
These are conversations and questions we need to have. We can no longer ignore these issues. We must engage and find out what these potential customers want, and then provide them in the channels and processes they use.
This is the gist of the New Model of Distribution.
But, that’s not all. We intend to weave in incentives and policy where those will assist the move toward greater deconstruction and more reuse. We are engaging cities and counties in America with our Deconstruction Policy Accelerator™.
Education will be a large part of the puzzle, as well. Organizations like Build Reuse, All for Reuse, CR0WD, Delta Institute, ReCapturit webinars, and other sources will be needed.
Here are some additional bright spots now available along this path to the New Model:
- Scanning, measuring, categorizing, quantifying, and valuing materials in existing buildings.
- Adaptis.ai – “For Optimized Decarbonization And Reuse” – “Our tools help building owners and AEC professionals reduce energy needs and emissions, minimize the embodied carbon of construction, divert waste from landfills and extend building life.” – https://adaptis.ai.
- LiDAR – Light Detection and Ranging technology that can measure spaces and volumes and even identify materials.
- Architects’ tools:
- BIM – Building Information Management tools – these can be used to optimize buildings during design, measure performance, and can track material life cycles and effectiveness over time.
- REVIT® – Software by AutoCad® - “LiDAR data can be converted into a Revit file to automatically identify and measure waste material.” – Sustainability Consultant, Brandie Townsend.
- Automated robotic nail and screw removal - Urban Machine - https://urbanmachine.build/ - The robot cleans lumber on-site while the building comes down! New lumber made from old – instantly.
- Automated Lumber Grading – Soon we will be able to inspect and measure lumber for structural grades and keep the value at its highest for the lumber.- MiCROTEC - Viscan - https://www.microtec.us/products/viscan
- Reuse of structural steel members – Imagine the energy it takes to transport steel members to a steel mill and melt it. Why not use beams as beams and columns as columns and save melting them and making new ones?
- Heyne-Tillett Steel –
- KL&A Engineers and Builders –
- Boulder, CO USA
- https://www.klaa.com/
- By reusing and recycling building materials, less waste is sent to landfills, incinerators, or oceans, where it can pollute the air, water, and soil, and contribute to climate change.
- Automated Sorting and Processing Technologies: Utilizing advanced automated sorting technologies such as robotic arms, machine learning algorithms, and computer vision systems to sort and process used materials, ensuring high efficiency and accuracy in the sorting process.
- Community Development: Affordable reclaimed materials can be used to build community centers, affordable housing, and other infrastructure, fostering a sense of ownership and pride within these communities.
- Access to Resources: By reusing materials, communities can have better access to building resources, which may have been previously unaffordable or inaccessible.
- Improving the health and well-being of residents, especially for those who live in substandard or overcrowded housing conditions that may expose them to hazards such as mold, lead, asbestos, or pests. By reusing and recycling building materials, more safe and comfortable housing options can be created or renovated, which can enhance the physical and mental health of residents, as well as their social and economic opportunities. Additionally, deconstruction typically introduces far fewer contaminants into the community because of its low-impact methods, as opposed to demolition, which can spread contaminants and dust for blocks.
- Improving the health and well-being of residents, especially for those who live in substandard or overcrowded housing conditions that may expose them to hazards such as mold, lead, asbestos, or pests. By reusing and recycling building materials, more safe and comfortable housing options can be created or renovated, which can enhance the physical and mental health of residents, as well as their social and economic opportunities.
Further down the path, but not too far away, there will be rich data available, made available by the new means to identify and label, and to track materials flows:
- Blockchain can be used to create a transparent and secure system for tracking the origin, quality, and quantity of used building materials. This can help in establishing trust between different parties involved in the supply chain and ensure the authenticity of the materials.
- Internet of Things (IoT) devices can be used to track and monitor the movement of used building materials throughout the supply chain. Sensors and RFID tags can provide real-time data on the location, condition, and availability of these materials, enabling better inventory management and logistics planning.
- Big data analytics can be employed to analyze historical data related to the usage and availability of used building materials. This can help in predicting demand, optimizing inventory levels, and identifying opportunities for reusing materials in new construction projects.
- Artificial Intelligence (AI) can be utilized for predictive maintenance of used building materials, identifying potential defects or weaknesses in reclaimed materials, and optimizing the selection of materials based on specific project requirements.
The list goes on!
Let’s sum this up. We must address these three needs:
- Multiples of current volumes
- Greater processing and storage capacity
- Modern systems implementation
We must recapture materials from ALL available sources:
- Demolition
- Construction Jobsites
- Deconstruction
- Urban Mining
- Discontinued, Overages, Returns, and Seconds as Inventory (DORSI)
We must establish connection and communication and develop relationships with the AEC community and begin to “speak their language.” We must do the work of “Customer Development” with architects, engineers, construction contractors, and building owners all being “customers.”
Incentives, policies, and education will all help.
We must embrace new technologies.
We must share what works! This is a community effort.
We must be mindful and respectful of people, process, and profits. I use the acronym PASES to keep in mind: Profit, Affected Stakeholder Empathy, and Simplicity.
We are building the New Model of Distribution of Recaptured Building Materials.
Waste Is Not Waste Until It Is Wasted.
Join us.
Larry